Est. 2013
Anti Static Epoxy Flooring
In today’s fast-evolving industrial landscape, ensuring reliable protection against static electricity is essential for maintaining safety and operational efficiency. Anti-static epoxy flooring offers an advanced solution to combat electrostatic discharge (ESD) in sensitive environments. This specialized flooring is designed to dissipate and control static electricity, safeguarding personnel, equipment, and sensitive materials in areas such as communication rooms, AGV trafficking floors, and other high-tech or critical spaces. Anti-static epoxy floors are crucial for industries like pharmaceuticals, automotive manufacturing, electronics production, and data centers. However, to ensure the flooring performs optimally and meets the specific requirements of each area, it is essential that it is installed by approved and trained professionals. Proper installation ensures the floor’s ability to adequately dissipate electrostatic charges and prevent potential damage or hazards caused by ESD. After installation, rigorous testing must be conducted to verify that the anti-static epoxy flooring meets the required standards and is aligned with the unique needs of the environment. By investing in a properly installed and tested anti-static flooring system, businesses can achieve reliable ESD protection while maintaining a safe and efficient workspace.
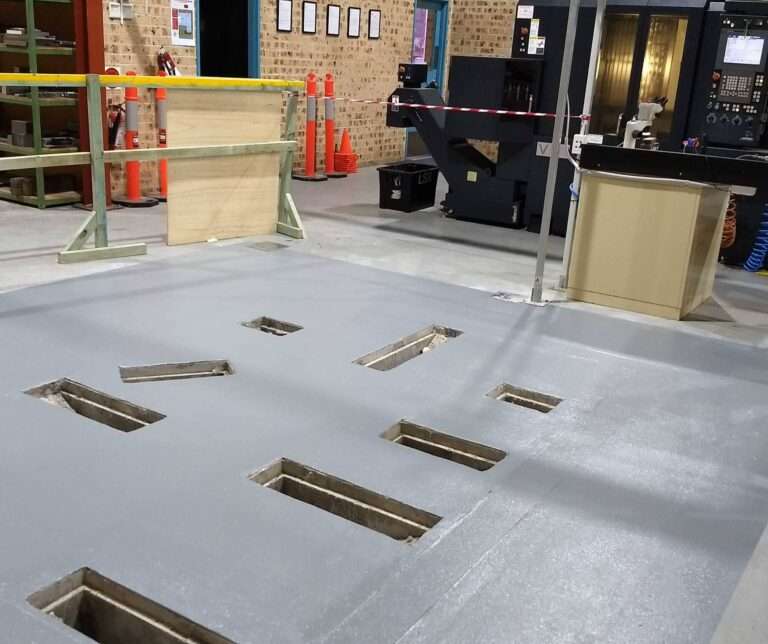
Features and Benefits of ESD Epoxy

Low Airborne Molecular Contaminants (AMC) emissions
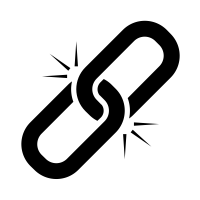
Very good mechanical resistance, High Performance
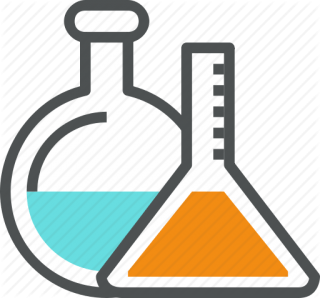
Good resistance to specific chemicals
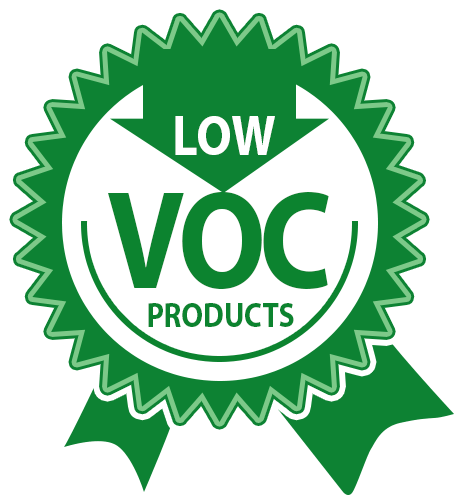
Low VOC emissions, Low odour, Environment friendly
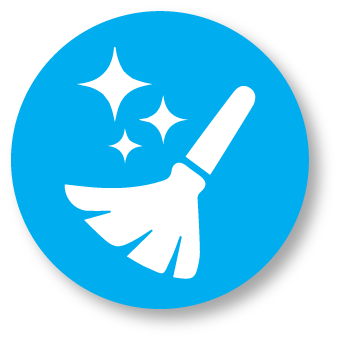
Easy to clean, Easy to maintain and refurbish

Provides reliable and long lasting ESD protection
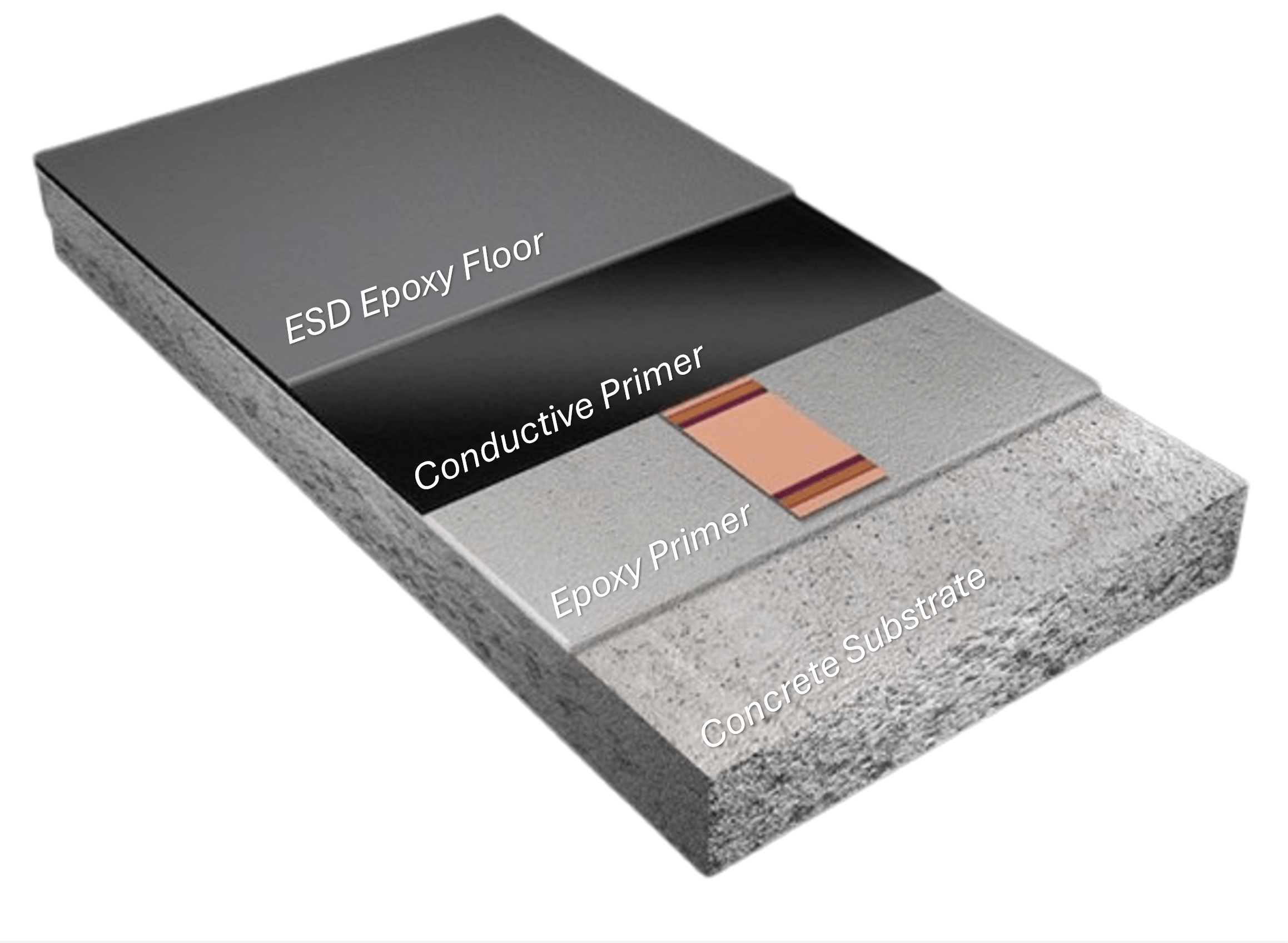
We Use Nano ESD Technology
At Atlas Coating we use the Nano ESD Epoxy System, a breakthrough in anti-static epoxy flooring technology. Unlike conventional systems, where conductive carbon fibers can settle at the bottom if applied too thickly, the Nano ESD system ensures uniform particle dispersion throughout the entire film. This eliminates performance issues caused by uneven static dissipation, making it more reliable and human-error-proof. Ideal for industries like electronics, healthcare, and data centers, our advanced dissipative epoxy flooring delivers consistent safety and durability. ESD epoxy floors are engineered for their specific purpose and performance, which is why they are typically available in standard grey only. However, we offer custom colors made to order based on your unique requirements. Ideal for industries like electronics, healthcare, and data centers, our advanced dissipative epoxy flooring delivers consistent safety and durability. Contact Atlas Coating to upgrade your space with cutting-edge anti-static floor solutions
ESD Epoxy Flooring Process
Floor Preparation
The purpose of floor grinding is to remove dirt and contaminants from the surface of the floor. as well as producing a Profile (CSP3) which is the desired roughness for achieving an optimal mechanical bond between the epoxy primer and the floor substrate. This ensures better adhesion and durability of the epoxy coating
Primer and Earthing point
After completing the floor preparation, a 100% solid content epoxy primer will be applied at a rate of 0.4 kg per square meter. Once the epoxy primer has cured, it is time to install the earthing point using copper stripes. Two points will be installed per room or per concrete slab to ensure sufficient discharge to the earth.
Conductive primer application
Now is the time to apply the conductive primer, which will improve conductivity and establish a dependable grounding system. This application guarantees the efficient dissipation of electrical charges, reducing potential risks. The conductive primer will be applied at a rate of 10 m² per litre.
Applying ESD coat
After applying the black conductive primer, we will use a trowel to apply a self-smoothing ESD epoxy. This will be followed by a roll-on topcoat ESD epoxy. Depending on our client's anti-slip needs, silica carbide can be added to the topcoat at this stage to achive any rating from P3 to P5
Regions we serve
Buckle up, folks! We’re on the move and bringing our top-notch epoxy flooring solutions to a variety of areas. From Sydney metro to Central Coats, Newcastle to Sutherland, and even Wollongong and Kiama, we’ve got you covered. So if you’re ready to revamp your floors, just give us a call – we’ll be there in a flash!
Our Warranty
We offer a 5-year industry warranty on all our products and services. This warranty covers peeling, delamination, lifting, and hot tire pick-ups. We stand behind the quality of our workmanship and materials, ensuring your floors remain in pristine condition for years to come. Contact us today for durable and reliable epoxy flooring solutions.

Recent Blog Posts
Frequently Asked Questions
Anti-static epoxy flooring is a specialized form of flooring designed to reduce static electricity buildup. It contains a conductive compound that accumulates static electricity to drain, ground, or dissipate any potential discharge. It’s commonly used in industries where static electricity could compromise electronic components, ignite flammable chemicals, or create an uncomfortable shock. These industries include electronics, pharmaceuticals, healthcare, and any environment dealing with flammable substances.
Anti-static epoxy flooring comes with numerous advantages. Firstly, it safeguards sensitive electronic equipment from static-induced damage, enhancing the longevity and operational efficiency of these devices. It also significantly reduces the risk of static-induced fire or explosion in environments dealing with flammable substances, thereby improving overall workplace safety. Moreover, this specialized flooring is highly durable and resistant to wear, tear, and chemical spillage, making it a cost-effective solution in the long run. Lastly, due to its seamless and glossy finish, not only does it enhance the aesthetic appeal of the space, but it also becomes easier to clean and maintain, promoting better hygiene standards.
The installation process of anti-static epoxy flooring is a multi-step procedure that requires professional expertise. Initially, the underlying concrete floor is thoroughly cleaned and prepared to ensure optimal adhesion of the epoxy. Any existing cracks or imperfections are repaired, and the surface is then ground or shot-blasted to create a rough texture. Once prepared, a primer is applied to the surface to further enhance adhesion. Following the application of the primer, the conductive epoxy layer is installed. This layer contains the conductive elements that give the flooring its anti-static properties. After the epoxy layer has fully cured, a conductive copper strip is installed around the perimeter of the room, connecting the floor to an earth ground. Finally, a top sealant layer is applied to protect the floor and provide a clean, shiny finish
Anti-static epoxy flooring effectively stops the buildup of static electricity by incorporating a conductive compound within its formulation. This compound forms a network of channels that allow the static electricity to flow through the floor towards a grounded point, usually a copper strip installed during the floor’s assembly. As a result, the electric charge is safely dispersed, preventing the buildup of static energy. Therefore, the risk of static electricity discharges, which can cause damage to sensitive electronic equipment and potentially cause fires in flammable environments, is significantly reduced.
There are several types of anti-static epoxy flooring available in the market catering to different needs and requirements.
- Epoxy Anti-static Floor: This type is typically used in areas where static-sensitive electronic components are handled. It features an extra layer of static-control compound, ensuring resistant to electrostatic discharge.
- Polyurethane Anti-static Floor: Known for its durability and resistance to chemicals, this type is often recommended for pharmaceutical environments, laboratories, and places where high hygiene standards are required.
- Vinyl Anti-static Floor: This type is known for its aesthetic appeal and is commonly used in office spaces, schools, and hospitals. Its anti-static properties prevent damage to electronic equipment and reduce the risk of electric shock.
Anti-static epoxy flooring requires relatively minimal maintenance to keep it in optimal condition. Routine cleaning, which includes sweeping and mopping, is essential to prevent the accumulation of dust and debris that could potentially affect the floor’s anti-static properties. It’s recommended to use a neutral pH cleaner to avoid damaging the floor coating. Periodically, a more thorough cleaning may be necessary to remove any ground-in dirt or grime. In terms of durability, these floors are designed to withstand heavy traffic and harsh conditions, but if any damage occurs, it should be addressed promptly to maintain the floor’s protective properties. Regular inspections can help identify any areas that may require repair or recoating. Despite the low maintenance, it’s critical to follow the specific care instructions provided by the flooring manufacturer.
Regarding health and safety considerations, anti-static epoxy flooring is generally considered safe. However, during the floor installation process, adequate ventilation should be ensured as the epoxy can release fumes that might be harmful if inhaled in large quantities. Once installed and cured, the floor poses minimal health risks. In terms of safety, the flooring is designed to be slip-resistant, thus reducing the risk of accidents. However, in areas prone to wet conditions, additional anti-slip measures may be required. Additionally, regular maintenance of the floor’s anti-static properties is crucial to prevent any potential electrical accidents. Always ensure that the flooring is installed and maintained by professionals to ensure optimal functionality and safety
The lifespan of anti-static epoxy flooring can significantly vary depending on factors such as the quality of the material, the installation process, and the level of traffic and usage it endures. However, with proper installation and regular maintenance, this type of flooring can typically last anywhere from 5 to 10 years. It’s worth noting that industrial or commercial areas with heavy traffic might experience a shorter lifespan. Therefore, regular inspections and prompt repair or recoating of any damaged areas are crucial to extend the floor’s longevity.
Choosing the right type of anti-static epoxy flooring involves several key considerations. First, identify the nature and level of static electricity in your environment. This can be determined by factors such as the type of equipment used, the volume of electronic devices, and the level of foot traffic. Second, consider the physical conditions of the place where the flooring will be installed, such as the level of moisture, temperature, and existing floor condition. Third, examine the durability needs based on the frequency and type of traffic the floor will endure. Finally, consider your budget as the costs can vary significantly across different types of anti-static epoxy floorings. Always consult with a professional flooring contractor to ensure you make an informed decision.
One of the main challenges with installing anti-static epoxy flooring is ensuring proper adhesion to the substrate. Any contaminants, such as dust or moisture, can hinder this process and result in a weaker bond. Therefore, it’s crucial to properly prepare the surface before installation by thoroughly cleaning and repairing any damages. In some cases, additional measures may need to be taken, such as