Est. 2013
Workshop Epoxy Flooring
Diamond grinding is a crucial step in achieving successful epoxy flooring in workshops. The purpose of diamond grinding is to create a CSP3 profile, which provides the necessary roughness for a proper mechanical bond.
We invite you to watch our video showcasing the process of grinding a mechanical shop floor in Hornsby, as we prepare it for a durable and brand-new epoxy flooring solution that will stand the test of time.
Features and Benefits of Epoxy Flooring in Workshop

Non Slip
Epoxy coatings are available in various levels of slip-resistance, conforming to all industry standards.
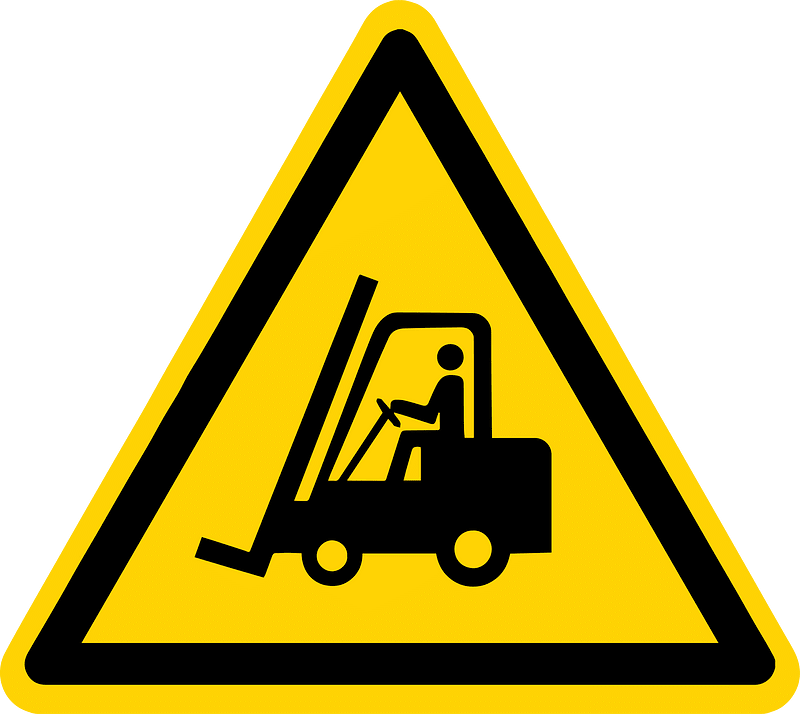
High Performance
Epoxy is well-suited for high traffic areas that are subject to impact from heavy vehicles and extreme wear.
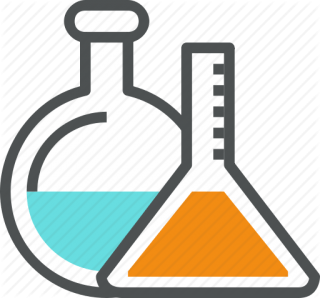
Chemical Resistance
Epoxy flooring coatings are known for their seamless finish and exceptional chemical resistance.
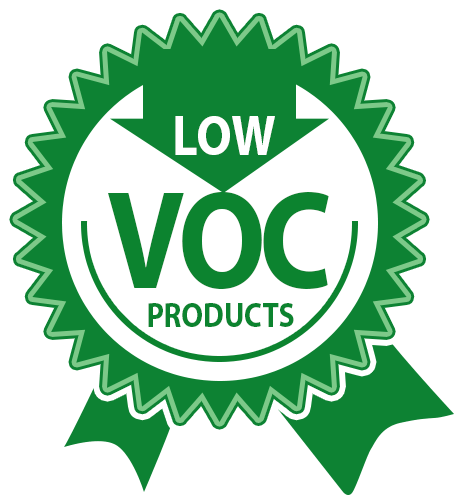
Low VOC
Low VOC emissions, Low odour, Environment friendly. Safe for People and animals
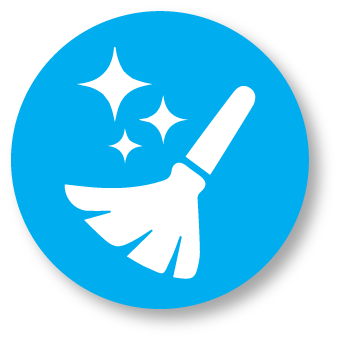
Easy to clean
Epoxy floor coatings provide concrete with dust-proofing and create a seamless, easy-to-clean surface
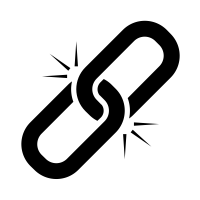
Long Lasting
Epoxies with high solid content are resilient and durable, offering protection against impact and excessive wear.
Our Solutions for your Workshop Floor

2 Coats Roll On Epoxy
The application of two coats of roll-on epoxy in workshops offers a cost-effective solution, providing durability, chemical resistance, and an appealing finish, all while keeping expenses in check.
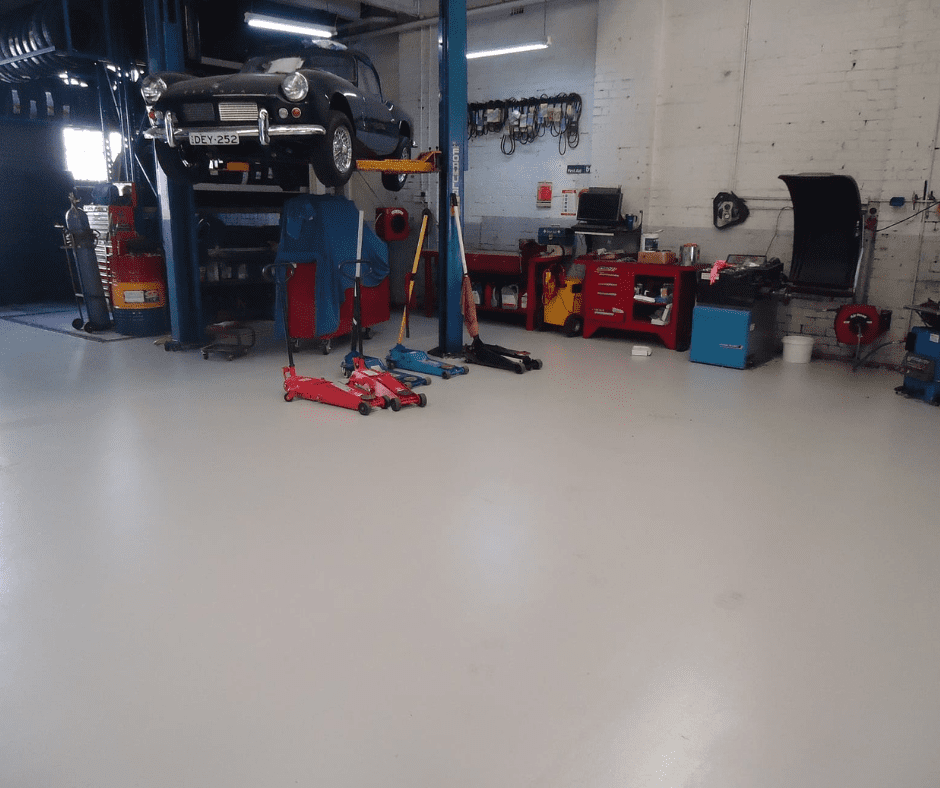
3x Coats Roll On System
The three-coat epoxy roll-on system for workshop floors provides exceptional durability, chemical resistance, and a polished finish. It ensures long-lasting protection against heavy foot traffic and is ideal for high-traffic environments.

High Build Epoxy System
High build epoxy is the ultimate solution for workshops, offering exceptional resistance to high impacts. Its anti-slip properties provide a safe working environment while ensuring long-lasting durability and protection against heavytraffic.
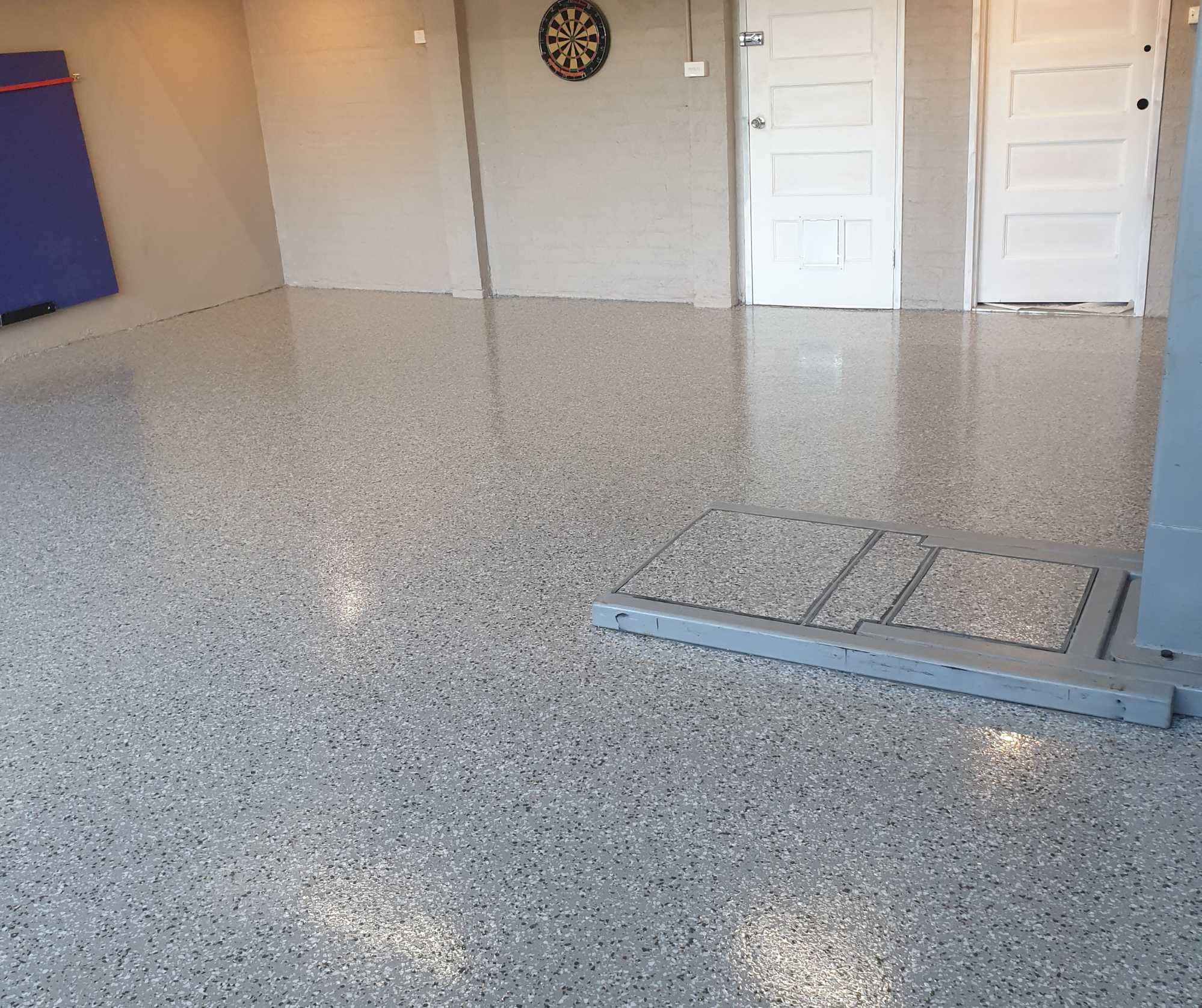
Epoxy Falke System
The full flake epoxy system brings numerous benefits to workshops. Its unlimited design options allow for customisation, while providing durability, chemical resistance, and a visually striking finish that enhances the workspace.

Anti Slip Epoxy
In workshops, ensuring a safe working environment is of utmost importance. That's where anti-slip epoxy comes into play. Our specially formulated epoxy uses aluminum oxide #60, an incredibly hard-wearing material, to achieve a P4-P5 anti-slip rating.
This means that it provides excellent traction and grip, both for people and vehicles. By incorporating this anti-slip technology into our topcoats, we aim to minimize the risk of accidents caused by slips or skids.
With our anti-slip epoxy, you can rest assured that your workplace will be safer, allowing employees and vehicles to navigate with confidence. Safety is our top priority.
Our Warranty
we offer a 5-year industry warranty on all our products and services. This warranty covers peeling, delamination, lifting, and hot tire pick-ups. We stand behind the quality of our workmanship and materials, ensuring your floors remain in pristine condition for years to come. Contact us today for durable and reliable epoxy flooring solutions.

Recent Blog Posts
Frequently Asked Questions
Workshop epoxy flooring is a type of industrial flooring system that uses epoxy resin as the main component. Epoxy resin is a durable, adhesive material that can withstand heavy traffic and resist chemicals, making it ideal for workshop environments where there is constant movement of heavy machinery and exposure to harsh substances.
The installation process for workshop epoxy flooring involves several steps. First, the surface of the workshop floor is thoroughly cleaned and prepared to ensure proper adhesion of the epoxy resin. Any cracks or imperfections are also repaired at this stage.
Next, a primer coat is applied to the floor to create a strong bond between the concrete and epoxy resin. This helps to prevent any air pockets or bubbles from forming during the application process.
Once the primer has dried, the first layer of epoxy resin is poured and spread evenly across the floor using specialized tools. This layer is then left to cure for a certain period of time before another layer is applied. The number of layers needed depends on the desired thickness and durability of the flooring.
After the final layer has been applied, a topcoat is added to provide extra protection and enhance the appearance of the workshop floor. This can be in the form of a clear coat or a colored coating, depending on the preference of the owner.
The entire installation process can take anywhere from 2-3 days, depending on the size and condition of the workshop floor. Once completed, the epoxy flooring will continue to cure and harden for several more days before it can withstand heavy traffic and chemical exposure.
Epoxy flooring is relatively easy to clean and maintain, making it a popular choice for workshops and other high-traffic areas. Regular sweeping or vacuuming can help remove dirt and debris from the surface. For tougher stains or spills, a mild detergent mixed with water can be used to spot clean the affected area. It is important to avoid using harsh chemicals or abrasive cleaners as they can damage the epoxy coating. Additionally, it is recommended to regularly reapply a topcoat every few years to maintain the shine and durability of the flooring.
Yes, epoxy flooring can be formulated with anti-slip additives to provide a safer surface for high-traffic areas. This is especially beneficial in workshops where spills and wet floors are common. The level of slip resistance can also be customized according to the specific needs of the space.
The lifespan of epoxy flooring in a high traffic area, such as a workshop, can vary depending on the quality of installation and maintenance. Generally, with proper care and regular topcoat applications, epoxy flooring can last up to 15-20 years. However, heavy machinery or equipment may cause more wear and tear, potentially shortening the lifespan of the flooring. It is important to consult with a professional installer for the best care and maintenance practices for your specific space. Overall, epoxy flooring is a durable and long-lasting option for high traffic areas, making it a popular choice among many industries.
Epoxy flooring is highly resistant to grease, oil, and battery acid. This makes it a popular choice for workshops and garages where these substances are commonly present. The seamless and non-porous surface of epoxy flooring prevents these substances from seeping into the floor and causing damage. In addition, spills and stains can be easily wiped away without leaving any lasting effects on the flooring. This is why epoxy flooring is a preferred option for spaces where cleanliness and chemical resistance are important factors.